The tubular heating elements are manufactured according to KANTHAL – OAKLEY technology, utilizing the latest patents and solutions from CSM and Kanthal/Granlund machines and equipment. High longevity and reliability are ensured by the use of high-quality materials: magnesium oxide, premium resistance wires, and protective tubes in accordance with the specified standards for the heating industry. Our electric heating elements meet the requirements of DIN EN 60335-1 (VDE -700-1), and are certified for CE and VDE marking.
Nominal voltage and power rating
The voltage range used: 12V…480V.
Typical voltages used: 24V, 48V, 115V, 230V, 400V, 440V.
The power rating of the heating element is selected individually based on the operating conditions and length.
Power tolerance according to DIN EN 60335-1 standard is +5% to -10%. Upon special request, tolerance of ±5% is available.
Standard lengths of dead zones: 40 / 60 / 80 / 100 / 120 / 150 / 180 / 200 … 1000mm.
Heater element tube lengths:
Material of the protective tube | Heater element diameter | ||||
---|---|---|---|---|---|
6,4mm | 8,5mm | 10mm | 12mm | 16mm | |
Stainless steel | 200-3350 | 200-4900 | 250-5200 | 250-5200 | 250-6000 |
Tolerance of heater element diameter:
Tolerance of heater element length:
Table of used materials:
EN | AISI | Max. operating temperature of the material |
---|---|---|
1.4301 | 304 | 450°C |
1.4541 | 321 | 550°C |
1.4404 | 316L | 450°C |
1.4571 | 316Ti | 500°C |
1.4828 | 309 | 950°C |
1.4876 | Incoloy 800 | 1050°C |
2.4858 | Incoloy 825 | 1100°C |
Selection and application of tubular heating elements:
When selecting a heating element, it is necessary to define the following parameters:
When selecting power, it is necessary to consider the permissible maximum loads depending on the operating conditions:
Operating Environment | Material | |
---|---|---|
AISI 316L, 316Ti, 321 | Incoloy 800, 825 | |
Stagnant water | 10 | |
Moving water | 14 | |
Flowing water | 25 | |
Steam generators | 6 | |
Thin oil | 3,5 | |
Thick oil | 1,2 | |
Still air | 5 | 6 |
Moving air v=3m/s | 6 | 7 |
Moving air v-9m/s | 9 | 9 |
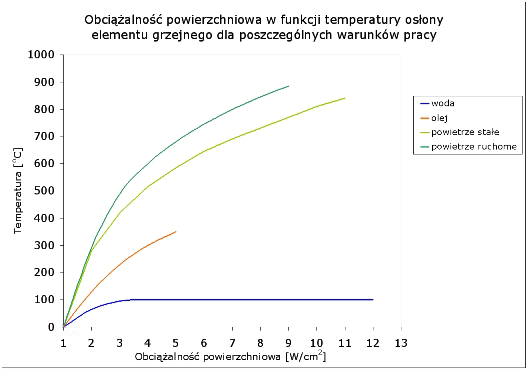
Mounting of Heating Elements:
To install a single tubular heating element, we use mounting sleeves that ensure a secure and safe installation in the working environment.
Currently, there are over a hundred different types of mounting sleeves available. We also produce custom mountings specifically tailored to customer orders.
Mounting Sleeves | |
---|---|
Material | Plain galvanized steel, brass, AISI 303, AISI 304 |
Thread | M10, M12, M14, M16, M18, M20, M22, M24 |
Mounting Method | Clamping, Hard soldering |
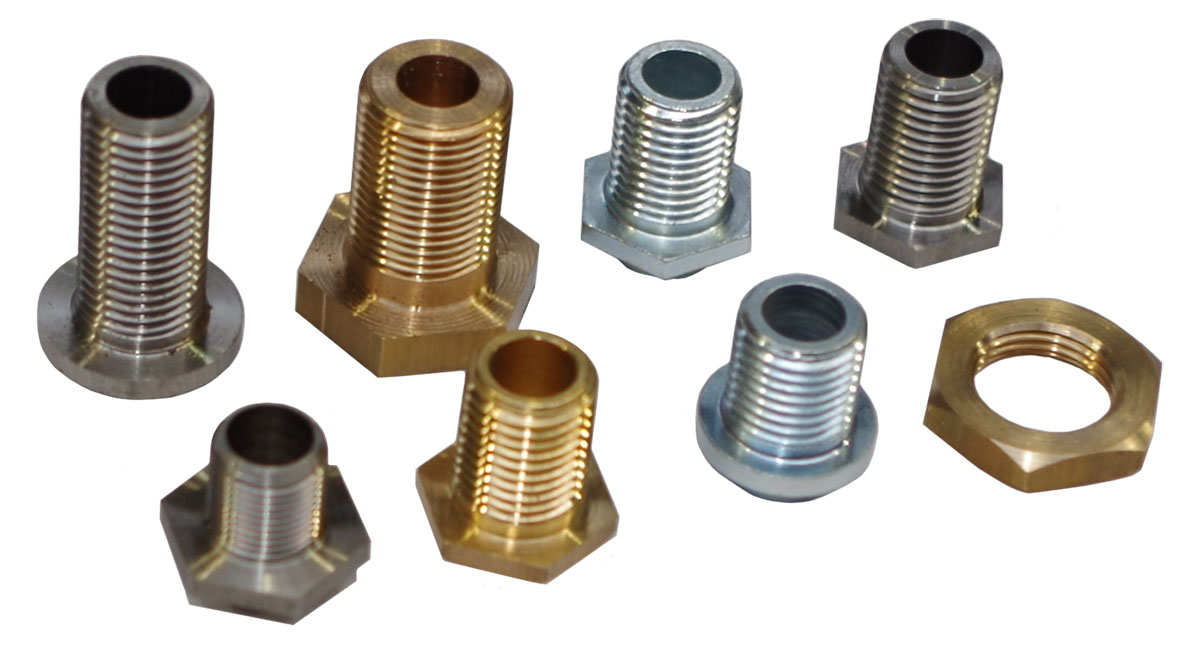
When mounting several individual heating elements close together, we typically use heads/collars with a specified thread.
These heads/collars provide easier installation and better functionality (e.g., electrical connections).
Mounting Heads / Collars | |
---|---|
Material | Brass, stainless steel AISI 304, AISI 316L (available upon request), plain steel ST |
Thread | G1″ – G2 1/2″ |
Mounting Method | Hard soldering 45Ag (56Ag available upon request) |
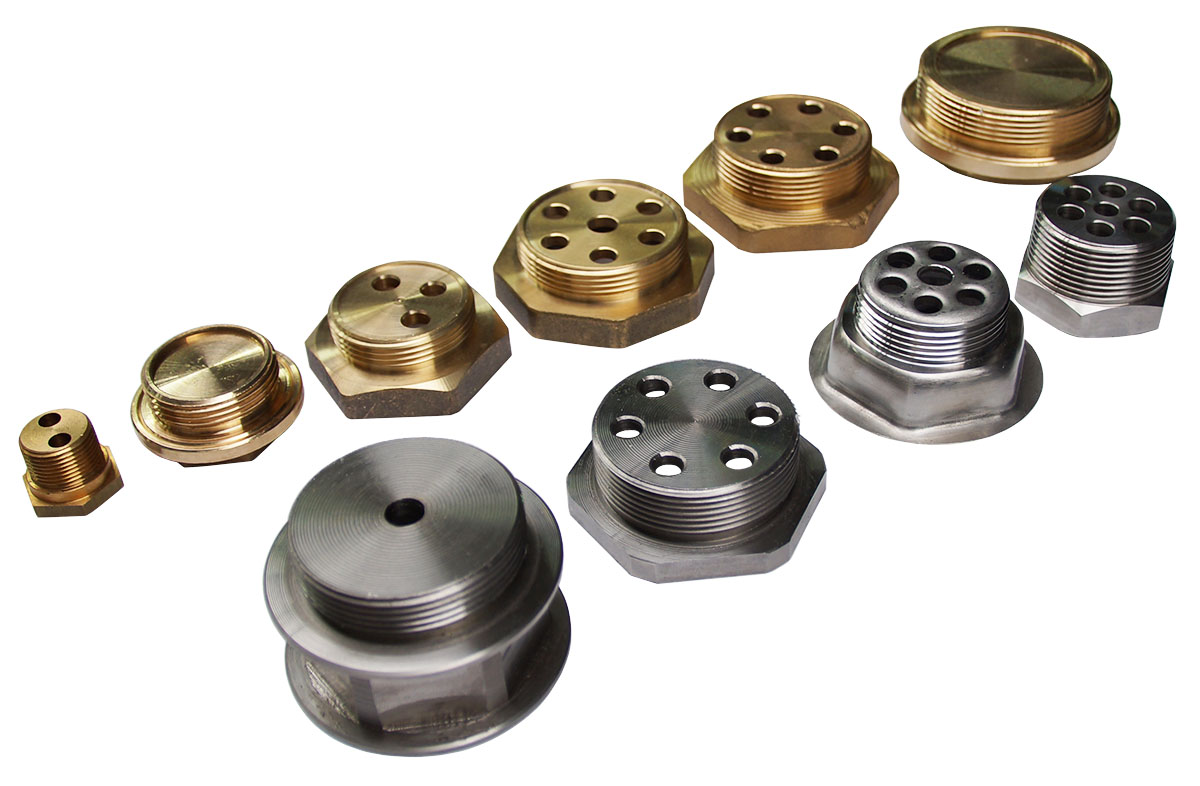
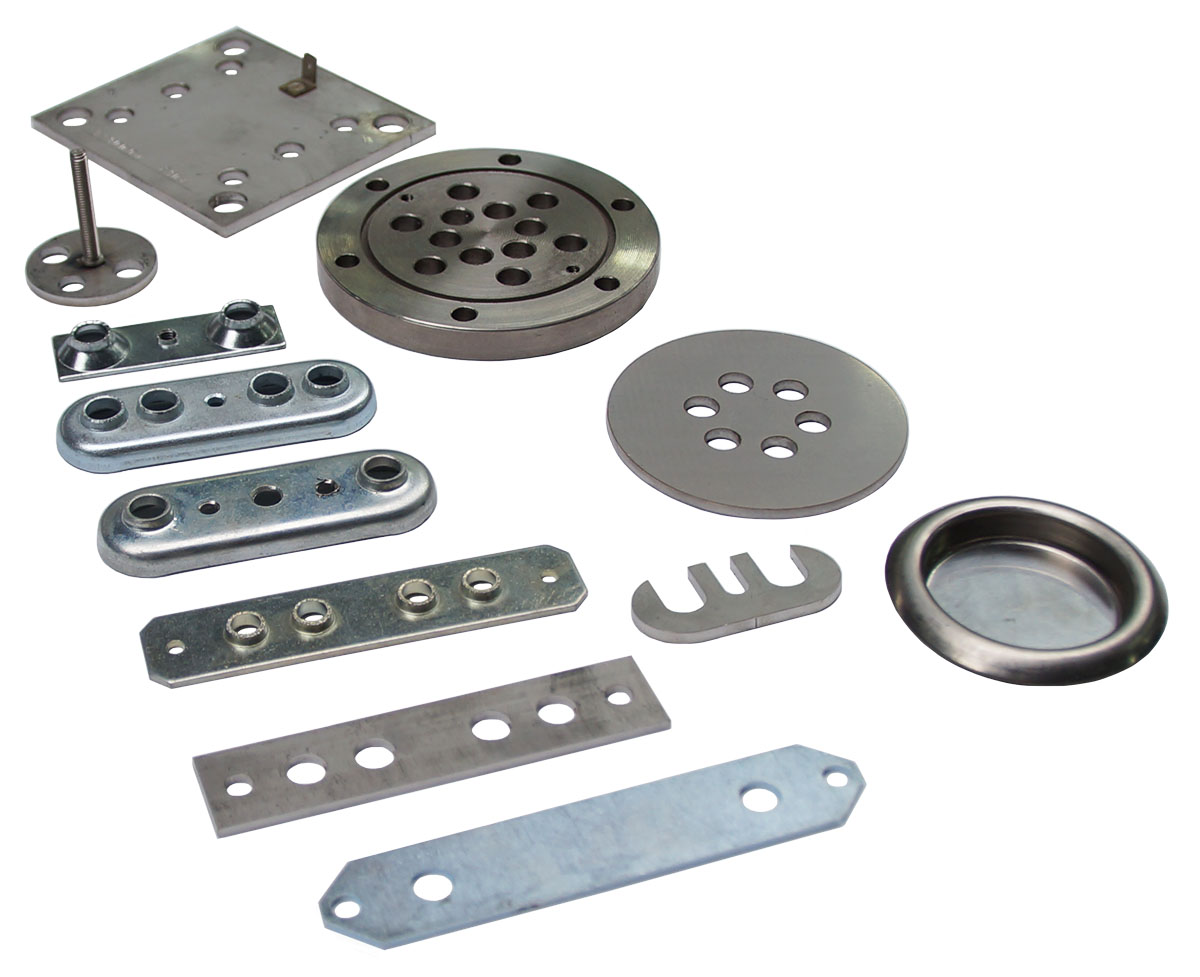
Depending on the size of the head/collar, it is possible to mount up to 6 individual heating elements at once.
An additional mounting method for heating elements includes special mounting plates, round flanges (Dmax=500mm), rectangular flanges (max. 600x400mm), square flanges (max. 400x400mm), protective tubes, etc., all custom-made upon request.
Electrical Terminals:
For tubular heating elements, the following electrical terminals are used: